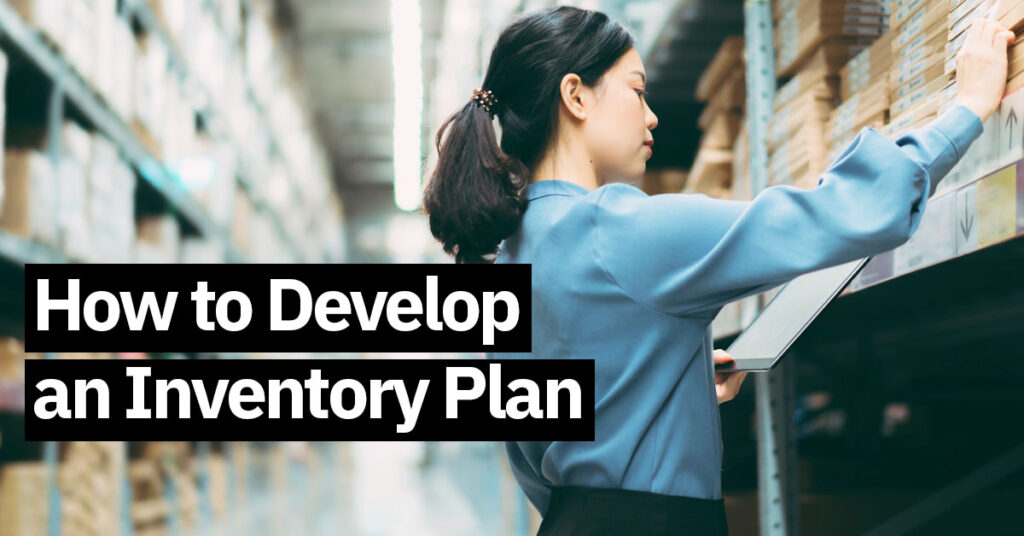
How to Develop an Inventory Plan
Inventory management is a critical aspect of any business that deals with physical products. Effective inventory management can help businesses optimize their operations and minimize costs. This article will explore how to develop an inventory plan and the best practices for effective implementation.
1. Department Coordination
Inventory management involves tracking the inventory levels of a business and ensuring that the right amount of inventory is available at the right time. This requires careful planning and coordination between different departments within a business, including sales, production, and procurement.
2. EOQ – Economic Order Quantity
One of the key principles of inventory management is the idea of the economic order quantity (EOQ). EOQ is the optimal order quantity that minimizes the total inventory management cost and considers the costs of ordering, holding, and running out of stock. By calculating the EOQ, businesses can determine the most cost-effective order size and frequency.
3. ABC Analysis
Another important principle of inventory management is ABC analysis. This involves categorizing inventory items into three categories based on their value: A items are the highest value items that represent a significant proportion of total inventory value, B items are of moderate value, and C items are low-value items. By analyzing the value of inventory items, businesses can prioritize their inventory management efforts and focus on the items that matter most.
4. Forecast & Purchase Order Systems
Effective inventory management also requires accurate forecasting. Businesses need to be able to predict demand for their products to ensure that they have enough inventory to meet customer needs without overstocking. This involves analyzing historical sales data, market trends, and other impacting demands.
To implement effective inventory management, businesses should consider adopting automated inventory management systems. These systems can help track inventory in real-time and automate ordering and reordering processes. This can help businesses save time and reduce the risk of human error.
5. Optimization
In addition, businesses should regularly review and optimize their inventory management practices. This involves analyzing inventory levels, identifying areas for improvement, and implementing changes to improve efficiency and reduce costs.
In conclusion, inventory management is a critical aspect of any business that deals with physical products. By implementing the key principles of inventory management, businesses can optimize their operations and minimize costs. This requires careful planning and the use of automated inventory management systems by regularly reviewing and optimizing their inventory management practices but staying ahead of the competition and meeting customer needs.